PVC全自动配混料系统
产品特点:
--采用工控PC机与PLC结合的全电脑控制系统,可实现全程自动控制。
--储存多组配方生产统计、随机打印、实时动态临控、故障报警,多级密码保护等;
--采用美国托利多纹管式计量传感器和控制仪表,动态稳定,计量准确,动态精度±3‰;
--采用独特的防沾图层和均化结构的计量螺杆,消除了影响计量精度的因素。
--采用了独特的气囊式卸料装置,为您彻底消除粘性物料“架桥”的烦恼;;
--采用系统压力平衡式集中除尘系统,使每个泄露点的粉尘降低到量低。
--全封闭式物料输送系统,防止物料的二次污染和环境污染。
订购热线:13616209888
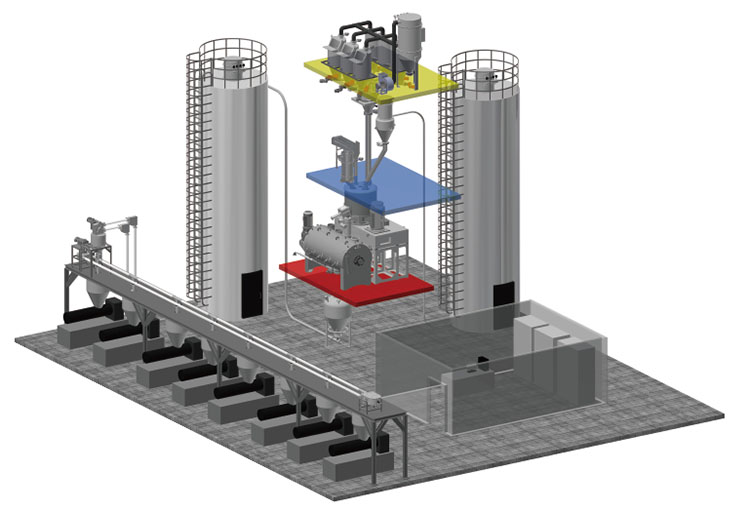
在PVC挤出加工行业中,传统的配混料方法是:热混、冷混加人工配料和输送。随着企业生产规模的不断扩大,这种方法已不能满足大批量生产的需要。
目前,一种较好的解决方案是:以电脑控制的自动配料系统为核心,辅以气力输送,再与热、冷混合机相结合,从而构成一套完整的PVC配料、混料生产线。与传统方法相比,新的方案具有很多明显优势,包括:
1. 由电脑控制的自动配料系统提高了配料精度,解决了人工配料的繁杂、物料的损失以及对操作者的化学危害等问题。
2. 高效的气力输送系统替代了大批物料搬运过程的繁重劳动,提高了生产效率。
3. 物料处理过程完全在封闭的管道中进行,避免了粉尘对车间环境的污染和对工人的危害。
4. 物料准备和处理过程更集中、更高效,产出量更高,完全可以满足大批量生产的需要。
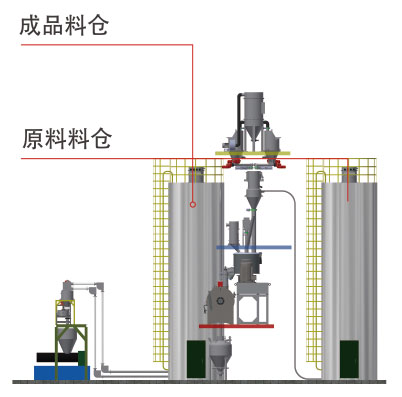

正压气力输送系统
PVC自动配料混料系统设备的配料过程
根据*终制品的不同,通常需要向PVC树脂中加入各种固体或液体助剂,如热稳定剂、润滑剂、增塑剂和着色剂等,并在一定的温度下使各组分与树脂充分混合、吸收,以获得配比准确、混合均匀且吸收充分的物料,这是生产高质量制品的前提。显然,配料过程是整个物料准备过程中耗时多、技术复杂且要求严格的阶段。因此,在现代配料技术中,都毫无例外地采用了由电脑控制的多组分自动称量计量系统。
实际上,配料过程就是要处理好各组分量的比例问题,因此,物料的计量是配料的核心。一般,计量方式有体积计量和重量计量两种。其中,重量计量由于采用了高精度的重量传感器对物料进行直接计量,因而更**、可靠,应用较为广泛。根据称重原理的不同,重量计量又可分为3种类型,即:分批次累加计重、失重式计重和流动过程物料的连续计重。其中,*适合PVC配混的是分批次累加计重,因为这种方式与混合机分批次混料的工作方式非常谐调。分批次累加计重的原理如图1所示。图中,A、B、C和D分别代表4种不同的组分(实际组分可以多于4种)。
在此所介绍的工业级重量传感器的静态精度可达1/1000以上,实际在配料系统中应用时的动态精度也可达到3/1000甚至更高,因此完全可以满足 PVC配料工艺的要求。但需要说明的是,在大多数配方中,由于PVC树脂和CaCO3所占比重较大,而其他各种助剂所占比重很小,因此,如果使用同一台称重装置,在较大的传感器量程内,易出现相对精度的下降,从而造成称量助剂时超差。为此,一般的做法是采用两台不同量程的称重装置分别称量,*后再汇总。
称重开始前,称重料斗4下面的阀门呈关闭状态,A、B、C和D各组分依次在螺旋加料器的作用下被加入料斗4中。当然,加入的量已事先在控制器6中设定完毕,因此,当每种组分被加到量时,控制器会将相应的电机停掉。*后,控制器将各组分的重量累加在一起,使其满足配方要求。称重结束后,控制器6会等待外界的控制信号,打开料斗4下面的阀门,以将物料放入下游设备。
控制器6的功能是将传感器的电信号还原为重量数值,并在电脑显示屏中显示。同时,根据要求对本系统中的电机和阀门等进行逻辑控制。除此之外,它还带有各种输入、输出接口,既可以接受其他部分的控制信号以实现联动,又可以将自身的称重数据实时地送到主控计算机进行处理。一般,该称重控制器同传感器一起,由专门的生产厂家供应。称重控制器和传感器除了具备上述*基本的功能外,有的还具有自动温度补偿、加料电机的变速控制、加料悬浮值的自动纠正以及自动校秤等功能。
图3 硬制品配混料的基本工艺流程
PVC的混合
PVC和助剂的混合一般由高速混合机和冷却混合机共同完成,部分软制品的生产也可只采用高速混合机。随产品的不同,混合时间和混合温度也各不相同。一般,混料温度在80~130℃之间,硬制品会高些(110~130℃),软制品则相对较低(80~100℃)。每批料的混合时间以8~10min为宜。
在PVC和助剂的混合中,通常以高速混合机为主。混合过程不仅是物料小颗粒的分散过程,也是各组分之间在一定温度下相互渗透和吸收的过程。因此,混合机内温升的均匀性是确保获得高质量混料的关键。在此,合理的搅拌浆设计以及对搅拌浆端部线速度的*佳控制显得非常重要。
一般,高的混合速度有利于物料的分散,但速度过高也会造成混合机内局部区域过热,造成物料温升不匀而影响混合料的质量。根据经验,*好将高速混合机搅拌浆的端部线速度控制在35m/s以内。此外,由于在混合过程中会产生大量的水汽,这些水汽凝结成水后又会落到混合机内,从而影响混合料的质量,因此,为混合机设计一个合理的排气系统也非常必要。
PVC自动配料混料系统设备,要想检验混合料的质量,可采用下述方法:
1. 视觉观察:质量好的混合料颜色正常,无杂质,无结块。
2. 堆密度测量:正确的混料过程会使物料的堆积密度增加。
3. 物料的流动性:准备一漏斗,在出料端装上插板阀。将一定量的干混料样品装入漏斗,打开插板阀,计算漏斗中物料完全排光所用的时间,时间越短意味着流动性越好。
4. 流动性能检测:好的混合料,其流动性也较好。
5. 颜色检验:一般应采用色度计检测颜色(尤其是白色),检测可分别在日光、紫外线、荧光和白光下进行。同时检测样品和标准品,即可测出样品是否合格。
6. 挤出样品:将干混料样品在一小型试验挤出机上挤出成试样,并检测:挤出过程中试样的尺寸稳定性;试样的表面和截面颜色;试样的表面质量;试样的抗冲击性能;挤出流动速率(单位时间的挤出重量);试样中是否含有杂质、异物;试样表面及截面是否有气孔。
在PVC加工行业中,通常可使用流变仪来测试干混料的质量,它可以测出扭矩和温度随时间变化的趋势曲线。利用专门的分析软件,可以推断出物料的流变特性、热稳定性、液体组分的吸收情况及增塑剂的吸收情况等。与标准曲线比较,即可找出干混料样的上述特性的偏离情况。由此,即可预先得知该干混料在挤出机中的加工特性,这对于控制*终制品的质量十分有利。
一般,由性能稳定的自动配料、混料系统生产出来的干混料,不要求对每一批料都做上述检测。对于白色型材,颜色的检验至关重要。
气力输送系统
在PVC的配料和混合过程中,以及在混合后向挤出机供料的过程中,采用气力输送来完成物料的搬运和传递是一种较好的方法。其优点是:输送量大、距离远、不受空间限制且易于实现自动化。
用于粉状物料的气力输送,按气流和气源的相对位置不同可分为压送式与吸引式两种,即常说的正压和负压。正压可以将物料从一处送往多处,负压则可以将物料从多处集中到一处。按气流状态的不同,气力输送也有两种方式:低压稀相输送和高压密相输送,它们的原理截然不同。
低压稀相输送是采用低压(几十kPa)高速气流(20m/s或更高)对物料进行输送。物料在输送管道中呈分散的悬浮状,并随气流向前流动。其缺点是:因气压较低,导致输送距离有限;对输送管道的布置有一定的要求;由于气流速度较高,因此对输送尾气的处理也有较高的要求。因此,它**于在输送量不大的情况下使用(5t/h以下)。其优点是:技术要求简单,设备维修方便且造价低。
高压密相输送采用的是高压(0.1MPa以上)低速的压缩空气。物料在输送管道中呈一段一段的塞状,并被压缩空气顶着向前低速运动。在要求较高的情况下,比如物料粘性较大、颗粒较小时,还应考虑采用带夹层的输送管道,并在夹层中补充压缩空气。其优点是:输送距离远,输送量大(可轻易达到10t/h以上),对尾气处理的要求较低。缺点是:技术难度较大,设备不易维修,造价也较高。
总之,上述两种方式各有优缺点,可视生产需要而决定采用哪种方式。
图2所示为典型的正压输送系统示意图。图中,物料通过旋转阀(旋转供料器)被放入输送管道中,然后被风机带来的气流吹送到目标料仓。目标料仓上安装有过滤器,用于排出干净的空气,并将物料留在料仓内。
物料的仓储
在大规模的物料处理过程中,仓储必不可少。PVC配混过程中的仓储可分为3种类型:树脂及各种助剂在混合前的仓储、混合过程中的仓储以及混合后、加工前的仓储。
树脂和各种助剂在混合前由于各自的物理特性不同,因此对仓储的要求也不同。卸料困难是仓储过程可能碰到的*大问题,涉及到卸料时物料的流动形式。理想的流动形式是整体流动,即出料口打开时,所有的物料颗粒都开始移动。能否形成整体流动取决于物料的特性和料仓底部的设计。一般,由于PVC树脂的流动性较好,颗粒较大,所以只要将料仓底部的锥角控制在60°范围之内,并尽量使料仓内表面平滑就可以形成整体流动。但需要注意的是各种助剂的卸料问题。一般,放料过程中会形成中心空洞,或者起拱(架桥),这种状态通常会严重影响后续流程的进行。为此,除了要合理地设计料仓结构外,还应配备强制破拱设施。常用的破拱方式包括:气动式、振动式和机械卸料器。
气动式破拱装置有多种,如:在料仓的弹性夹层中通入脉冲压缩空气,或者直接将压缩空气导入到可能产生架桥的部位。振动破拱方式也有多种,*常用的是 “仓底活化器”式,即通过料仓底部的整体振动达到破拱的目的。对于特别难以排放的物料,则可以采用专用的、安装于料仓内部的机械卸料器。
混合过程中的仓储除了要注意上述问题外,还应考虑流量平衡。要合理设计料仓容积,既不能过大造成浪费,也不能过小造成断流。
混合后、加工前物料的仓储也有严格的规定。在容积的设计上,要充分考虑生产工艺的需求,同时还要防止物料的结块和离析(粒度不均的物料进入料仓后,会出现粗细颗粒分层的现象)。
工艺流程设计
以上简要介绍了全自动配混料系统的各主要组成部分。在实际生产中,还要考虑如何将这几大部分有机地结合起来,以构成一个完整的系统,这就涉及到工艺流程的设计问题。
工艺流程的设计准则是,在保证*佳配混生产的同时,还应根据使用者的资金和场地条件,做出合理安排。因此,工艺流程设计应根据用户的不同需求而量身订制。需要说明的是:要想建立一个成功的配料混料系统,在系统的设计、制造、安装和调试过程中,买卖双方应保持密切的沟通和交流。图3所示是硬制品配混料的基本工艺流程。
总之,随着我国塑料工业的发展,以及企业生产规模的不断扩大,先进的物料预处理系统必将得到广泛应用,相信国内的设备制造厂一定能够为此类应用提供先进可靠的设备。